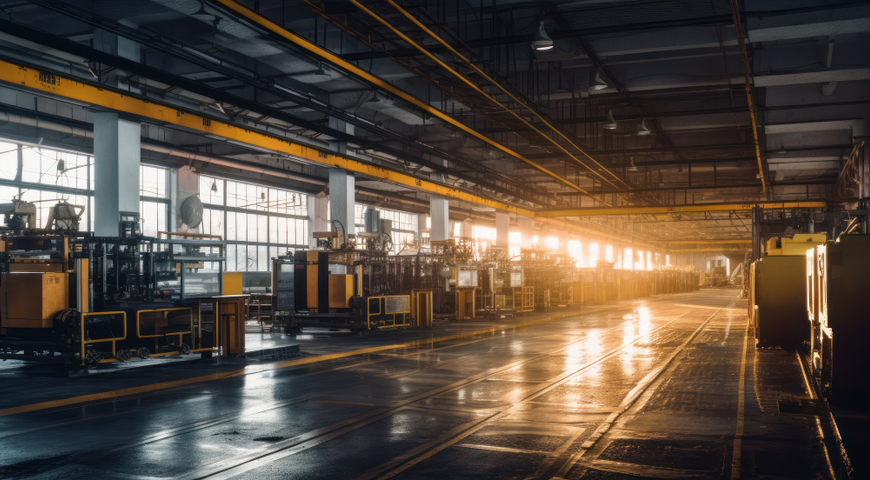
In the manufacturing industry, data backup, recovery and disaster recovery solutions play a crucial role in ensuring the continuity of operations and minimizing downtime. The maintenance of continuous uptime for factory floor operations is a critical driver of manufacturing business profitability since minutes of downtime can equal millions of dollars in lost sales, delayed revenues, wasted capacity, and higher fulfillment costs.
The challenge of maintaining near-100% uptime is exacerbated by the frequent lack of on-site tech support resources to address downtime sources like the failure of servers that control automated processes.
Other areas of the manufacturing business may have less sensitivity to momentary interruptions of operations, but still cannot afford extended downtime periods or loss of critical data due to cyberattacks, tech infrastructure failures, human error or natural disasters.
In particular, ransomware has grown in recent years to become the leading cyberthreat to manufacturing — wreaking costly data theft and downtime on businesses of every size. Ransomware attacks have become increasingly sophisticated and frequent, with cybercriminals wielding devious new tactics to get victims to pay for the restoral of their data and uptime.
With the increasing reliance on digital systems and the ever-growing volume of data generated, manufacturers need better and more powerful strategies to protect their critical information and recover swiftly in the event of a disruption.
Ideally, this should include data backup, recovery and disaster recovery solutions:
· Data backup involves creating copies of important data and storing them in secure locations. To ensure comprehensive protection, backups should be performed regularly — ideally in real time or at frequent intervals — using both on-site and off-site storage options. On-site backups offer quick accessibility for immediate recovery, while off-site backups provide added security against physical threats, such as fires or natural disasters.
· Recovery solutions are essential for promptly restoring data and systems in the event of accidental data loss, system failures or cyberattacks. In the manufacturing industry, where downtime can have severe financial implications, it is crucial to have efficient recovery mechanisms in place. This may involve employing data recovery software, implementing redundant systems and having a clear recovery plan that outlines the necessary steps and responsibilities. Regular testing and validation of recovery procedures are also vital to ensuring their effectiveness and to identify any potential vulnerabilities.
· Disaster recovery goes beyond data recovery and focuses on restoring overall business operations after a major disruption, such as a natural disaster, power outage or a cyberattack. Manufacturers can adopt a variety of measures, including redundant hardware and network infrastructure, alternate production sites and backup power systems. A comprehensive disaster recovery plan should address various scenarios, prioritize critical processes and establish communication channels to effectively coordinate recovery efforts.
Risks and threats: Understanding data protection in the manufacturing industry
The manufacturing industry faces several risks and threats to data that can jeopardize the integrity, confidentiality and availability of critical information — which can include product specifications, production data, supply chain information and customer records. Some of the key risks and threats include:
1. Cyberattacks: Manufacturers are increasingly targeted by cybercriminals seeking to exploit vulnerabilities in their systems. Malicious actors may launch ransomware attacks, data breaches or industrial espionage to gain unauthorized access to sensitive data, disrupt operations or steal valuable intellectual property.
2. Physical threats: Manufacturing facilities are susceptible to physical risks such as natural disasters, fires, power outages or equipment failure. These incidents can cause data loss, damage hardware and infrastructure and interrupt critical operations.
3. Insider threats: Employees or contractors with access to sensitive information can pose a risk to data security. Accidental or intentional actions by insiders, such as data theft, unauthorized disclosure or negligence in following security protocols, can lead to data breaches or compromise the integrity of manufacturing processes.
4. Supply chain vulnerabilities: Manufacturing often relies on complex supply chains involving multiple partners and suppliers. Any weak link in the supply chain can expose manufacturers to data breaches or disruptions. Third-party vendors may have inadequate security measures or inadvertently introduce malware or compromised components into the manufacturing ecosystem.
5. Data loss and corruption: Human error, technical failures or software glitches can lead to data loss or corruption. Manufacturing organizations generate vast amounts of data and if not properly backed up or protected, the loss of this data can have significant consequences for production, quality control and decision-making processes.
6. Regulatory compliance: Manufacturing companies must comply with government-imposed or industry-specific regulations regarding data privacy, security and intellectual property protection. Failure to adhere to these regulations can result in legal and financial penalties, as well as damage to the company's reputation.
The importance of a data backup solution
To mitigate these risks and threats, manufacturers should have a data backup plan (supported by proven backup solutions and technology) for the following reasons:
1. Protection against data loss: Manufacturing companies generate vast amounts of data, including product specifications, production schedules, inventory management, customer orders and quality control records, that are essential for day-to-day operations and decision-making processes. Data loss can occur due to various reasons, such as hardware failure, human error, cyberattacks or natural disasters.
A data backup plan provides a safety net by creating copies of important data and storing them securely. This ensures that even if the original data is compromised or lost, the backup copies can be used to recover and restore the information.
2. Business continuity: In the event of data loss or system failure, a robust backup plan ensures that critical information can be quickly restored, minimizing downtime and enabling operations to resume promptly. This helps manufacturing companies maintain business continuity, fulfill customer orders and prevent significant financial losses.
3. Compliance with regulations: The manufacturing industry is subject to various regulations regarding data privacy, intellectual property protection and industry-specific standards. Having a data backup plan in place is crucial for complying with these regulations. It demonstrates the organization's commitment to protecting sensitive information, maintaining data integrity and meeting legal requirements. Compliance failures can lead to severe consequences, including legal penalties, reputational damage and loss of business opportunities.
4. Mitigation of risks and threats: The manufacturing industry is not immune to risks and threats such as cyberattacks, insider threats and physical disasters. By implementing a data backup plan, manufacturers can mitigate these risks and minimize their impact. Backups act as a safeguard against data breaches, ransomware attacks or equipment failures. In the event of a disruption, the backup data can be used to restore operations and minimize the associated risks.
5. Support for decision-making and analysis: Data plays a vital role in driving informed decision-making, process optimization and continuous improvement in the manufacturing industry. Accurate and reliable data is necessary for analyzing production trends, identifying inefficiencies and implementing quality control measures. A data backup plan ensures that historical data is preserved, enabling manufacturers to access and utilize valuable information for strategic planning, forecasting and performance evaluation.
Backup best practices in manufacturing
Data backup best practices for the manufacturing industry include implementing the following strategies:
1. Regular and automated backups: Perform regular and automated backups to ensure the timely protection of critical data. Consider the frequency of data changes and the impact of potential data loss to determine the appropriate backup intervals. Real-time or frequent backups are recommended for highly dynamic data.
2. Redundant storage: Utilize redundant storage options, both on-site and off-site, to enhance data availability and protect against physical threats, such as fires, floods or equipment failures. Employing a combination of local backups, remote backups and cloud-based storage ensures data resilience and quick recovery options.
3. Incremental and full backups: Use a combination of incremental and full backups to optimize storage space and backup duration. Incremental backups capture only the changes made since the last backup, reducing backup time and storage requirements. Periodic full backups ensure a complete copy of the data is available.
4. Data encryption: Implement encryption for backups, both during storage and transmission, to safeguard sensitive data. Encryption helps protect against unauthorized access and data breaches, ensuring data confidentiality and compliance with privacy regulations.
5. Off-site backup: Maintain off-site backups to protect against site-specific disasters or physical threats that could impact on-site backups. Off-site backups should be stored in secure locations, preferably geographically separate from the primary data center.
6. Regular testing and validation: Perform regular testing and validation of the backup processes and data restoration procedures. This helps ensure the integrity of the backup data, identify any issues or gaps in the backup strategy and verify the effectiveness of the recovery process.
7. Documented backup and recovery plan: Develop a comprehensive backup and recovery plan that outlines roles, responsibilities, procedures and contact information for key personnel involved in backup and recovery operations. Documented plans help facilitate swift and efficient recovery during a crisis.
8. Security and access controls: Implement appropriate security measures and access controls for backup systems and storage locations to prevent unauthorized access or tampering with backup data.
9. Monitoring and alerting: Implement monitoring systems to track backup activities, validate successful backups and receive alerts in case of backup failures or issues. Proactive monitoring helps ensure the integrity and effectiveness of the backup solution.
10. Employee training and awareness: Train employees on data backup best practices, security protocols and the importance of data protection. Promote a culture of data awareness and responsible data handling within the organization.
By following these data backup best practices, manufacturing companies can enhance data protection, minimize downtime and ensure the availability and recoverability of critical information in case of a disruption or data loss event.
Data recovery best practices for the manufacturing industry
Data recovery best practices in the manufacturing industry involve the following key strategies:
1. Clearly defined recovery objectives: Establish clear recovery objectives and prioritize critical systems and data for recovery. Identify the recovery time objectives (RTOs) and recovery point objectives (RPOs) for different types of data to guide the recovery process and ensure that the most essential data is restored promptly.
2. Robust backup system: Implement a reliable and comprehensive backup system that aligns with the organization's recovery objectives. Regularly test and validate the backups to ensure their integrity and accuracy. Consider the use of redundant backup solutions, such as disk-based backups and cloud-based backups, to enhance data availability and recovery options.
3. Recovery testing: Regularly test the recovery procedures and validate the effectiveness of the recovery process. Conduct recovery drills and simulate different disaster scenarios to identify potential gaps or weaknesses in the recovery plan. Testing helps ensure that the recovery systems and processes work as intended and can be relied upon in an actual recovery situation.
4. Documented recovery plan: Develop a detailed recovery plan that outlines step-by-step procedures, roles and responsibilities for different personnel involved in the recovery process. Include contact information for key stakeholders and vendors to ensure clear communication during recovery efforts. A well-documented plan facilitates a coordinated and efficient response during a data recovery event.
5. Prioritized recovery: Prioritize the recovery of critical systems and data to minimize downtime and mitigate the impact of a data loss event. Identify the most essential production systems, customer data and intellectual property that need to be recovered first. This ensures that the most critical operations can resume quickly, reducing the impact on manufacturing processes.
6. Secure recovery environment: Ensure the recovery environment is secure and protected from potential threats. Implement appropriate security measures, including access controls, encryption and monitoring, to safeguard the recovered data and prevent unauthorized access or tampering during the recovery process.
7. Data validation and integrity checks: Validate the recovered data to ensure its integrity and accuracy. Perform data integrity checks, such as checksum verifications or data validation algorithms, to confirm that the recovered data matches the original data and has not been corrupted or altered during the recovery process.
8. Continuous improvement: Continuously review and improve the data recovery processes based on lessons learned from recovery drills, actual recovery events and emerging technologies. Regularly update the recovery plan to incorporate any changes in the IT infrastructure, systems or business requirements.
By following these data recovery best practices, manufacturing companies can enhance their ability to recover critical data, minimize downtime and ensure the resilience of their operations in the face of data loss or disruptions.
Common questions people also ask
What are the consequences of not having a data backup strategy?
Not having a data backup strategy for manufacturing companies can lead to disruptions in operations, production delays, missed delivery deadlines, customer dissatisfaction and potential loss of business. Permanent data loss may occur, compromising important information and intellectual property.
To put it another way, the absence of a data backup strategy puts the entire business at risk, impacting operational continuity, customer trust and overall competitiveness.
How often should manufacturers perform backups?
The frequency of data backups for manufacturers depends on various factors, including the volume of data generated, the criticality of the information and the acceptable level of data loss in the event of a disruption. Generally, manufacturers should aim to perform data backups on a regular basis to ensure data protection and minimize potential loss.
For critical data that is constantly changing, such as real-time production data or customer orders, frequent backups are essential. Ideally, these backups should be performed in real time or at regular intervals, ensuring minimal data loss in case of a failure. Continuous data replication or automated backup solutions can be employed to achieve this.
For less dynamic data, such as historical records or archived information, backups can be performed less frequently, such as daily, weekly or monthly, depending on the specific needs and risks involved. It is important to strike a balance between the cost of storage and the potential impact of data loss.
How long should it take to recover data after a disaster?
Ideally, a well-designed and tested disaster recovery solution aims for minimal downtime and a swift recovery. In some cases, recovery time objectives (RTOs) and recovery point objectives (RPOs) are defined to establish specific targets for data recovery. RTO refers to the maximum acceptable downtime, while RPO defines the acceptable amount of data loss.
For critical systems and data, organizations often aim for low RTOs and RPOs to restore operations quickly and minimize data loss. Depending on the infrastructure and the backup technologies in use, recovery times can range from minutes to hours.
What are the best backup solutions for manufacturing companies?
When it comes to backup solutions for manufacturing, it's crucial to consider the specific needs and requirements of the industry. Today’s backup solutions can be on-site, off-site, cloud-based or even a hybrid approach; but they should have the ability to quickly restore failed OT servers (regardless of the cause of downtime) as well as to restore to a variety of replacement servers for quickly getting mission-critical shop floor operations up and running.
For example, Acronis has a proven advantage in this scenario: the ability to restore failed factory floor process control servers in a matter of minutes from images of their OS, applications and data stored in local physical servers or virtual machines. Additionally, broad Acronis backup support for a range of common server operating systems, including legacy versions no longer supported by their vendors (e.g., Microsoft Windows XP), and rapid, unattended recovery capabilities like Instant Restore enable Acronis to deliver a unique competitive advantage in this scenario. When a process control server or automated manufacturing robot control server fails, Acronis can re-create a live, working replacement server on a local physical server or VM, reducing downtime to a matter of minutes.
Summary
Data backup, recovery and disaster recovery solutions are paramount for the manufacturing industry to protect valuable information, maintain operational continuity and minimize downtime.
By implementing robust strategies and regularly testing their effectiveness, manufacturers can ensure the resilience of their systems and mitigate potential risks associated with data loss or operational disruptions.
About Acronis
A Swiss company founded in Singapore in 2003, Acronis has 15 offices worldwide and employees in 50+ countries. Acronis Cyber Protect Cloud is available in 26 languages in 150 countries and is used by over 20,000 service providers to protect over 750,000 businesses.